Have you ever been caught scrambling for your disinfection records? Trying to tick off your employee’s training last minute? Or frantically attempting to get your quality scores up?
We all know how stressful it can be leading up to an external audit.
At SGA, we understand the scrupulous measures that quality assurance teams are faced with on a regular basis.
And so today, we’ll be discussing:
- What a quality assurance audit involves
- Common mistakes made leading up to an audit
- Our industry-leading strategies when it comes to audits
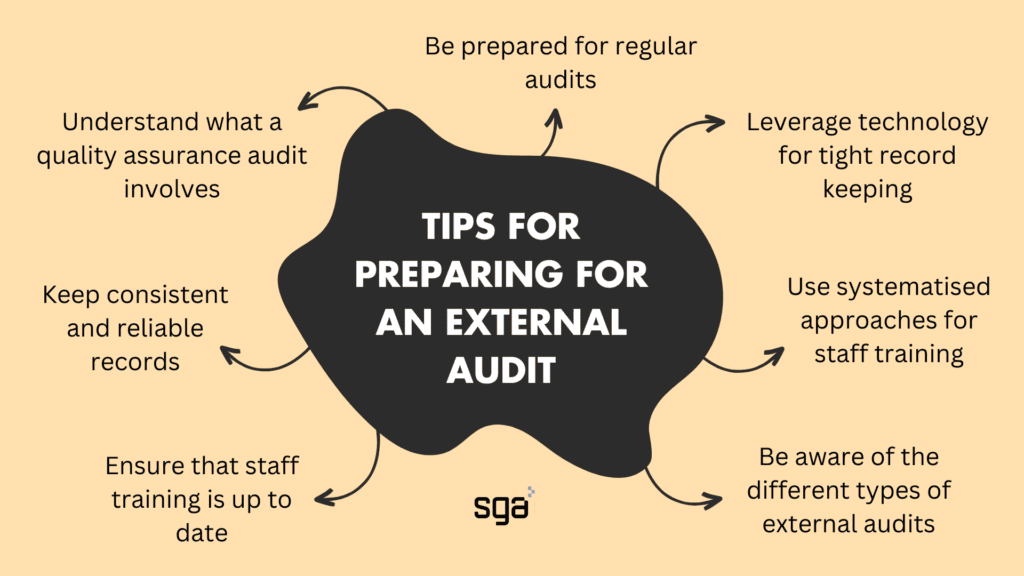
What Is A Quality Assurance Audit?
Quality assurance or external audits are a series of checks, measured against a set of standards.
These standards are established by an food distributer such as Coles or Woolworths, a governing body, such as BRC (British Retail Consortium), or 3rd party such as YUM!.
Audits are used in order to inspect and report on the quality of a facility.
How Often Can You Be Audited?
In the industrial disinfection industry, audits are performed very regularly.
Some facilities we work with are audited as often as every single week of the year.
At such a frequency, it is of vital importance that you are always prepared.
Biggest Mistakes When It Comes To External Audits
• Being Reactive
External audits can certainly spring up on you if you’re not organised and poor scores can be detrimental to a company’s reputation in the industry.
Perhaps the biggest mistake we see is quality assurance teams scrambling to get their facility up to standard in the days and even hours leading up to the audit.
This is not a sustainable approach and only leads to unnecessary stress.
• Not Keeping Records
Failing to keep consistent records can be detrimental to your facility’s quality assurance scores.
In recent times, auditors have become more stringent when it comes to long term quality performance and may even visit your facility unannounced.
They will not only look at the current state of your facility, but will also inspect your performance over time.
Not keeping reliable records only creates more work for you and your team.
• Neglecting Training
One of the biggest areas that quality assurance teams neglect is their training.
They focus so much on the cleanliness of the facility, that they forget that they are also being audited on their staff competency.
At the end of the day, your cleaners are your biggest asset. They ensure that the disinfection process is done to the best standard possible.
Thus, neglecting to keep them up to date on industry standards and procedures will result in poor quality scores when it comes time for auditing.
How We Stay Prepared For External Audits
Based on our 20+ years of industrial disinfection experience, SGA has developed an industry-leading audit preparation plan that we strongly believe can assist you.
We understand how stretched for time quality assurance manangers are, which can be make it difficult to find the time to focus on the long term.
So, just know that this framework hasn’t happened overnight. It’s been developed over years of trial and error.
It requires a proactive approach and will mean that you are always on the front foot when it comes to audits and relies on the following systems:
• Tight Record Keeping Using iAuditor
Each and every day, we leverage technology to help us keep accurate records of every clean we do.
iAuditor allows us to be agile and informed as we go. We can identify potential performance decrements as, or even before they happen.
We are able to immediately make changes to keep the best quality control in the industry.
• Up To Date Training Using Talent LMS
Keeping your cleaners up to date with the latest training is a mammoth task. Although it may seem cumbersome and at times overkill, we promise you it’s worth the investment.
We bring a systematised approach to our training using Talent LMS, which allows us to quickly identify when employees are approaching their training deadlines.
This not only helps us to achieve top scores in the training component of external audits, but also means our cleaners can be the most professional and competent in the industry.
Different Types Of External Audits
• Governing Bodies
Governing bodies, most notably the BRC (British Retail Consortium) are very well known in the industrial cleaning sector.
The are arguably the most stringent level of audit. This is because the audit is performed on meat that is going to be shipped internationally over longer periods of time.
• Food & Beverage Distributors
Next comes food distributers such as Coles and Woolworths which are the second most stringent.
Although these audits aren’t as hard as RBC, they still require a very high standard.
• 3rd Parties
Finally come 3rd party auditors such as YUM! and SQF (Sales Quality Foods), who service companies such as Dominos.
The Bottom Line
External audits are a regular and inevitable part of the industrial cleaning sector.
When it comes to audits, being on the front foot is going to hold you in extremely good stead, helping you avoid unnecessary, last minute stress.
Practically speaking, keeping your employees up to date with their training and updating that training after each audit to address any corrective actions needed will allow your team to not make the same mistake twice and stand on the shoulders of the expertise of the auditors. In addition, ensuring tight record keeping via your internal auditing software are certain keys to success.